Battery and sensor test center
The Research Center for Energy Storage Technologies at Clausthal University of Technology and the Fraunhofer Heinrich Hertz Institute operate a joint battery and sensor test center at the Battery Safety Campus Germany. This embodies a research infrastructure for testing high-performance battery systems that is unique in Germany in terms of its performance. With this infrastructure, the partners are prepared for future challenges when batteries for buses and trucks are no longer unusual and charging these batteries at 500 kW is no longer a rarity.
Batteries, especially for electromobility, are subject to very high requirements in terms of energy and power density, which is why highly integrated solutions are required. The high energy or power density also results in high heat source densities to be dissipated, which require particularly well thought-out thermal management. Demanding requirements are placed on battery and thermal management, particularly in borderline areas, such as the fast charging of batteries or with high dynamic loads and simultaneously high or very low ambient temperatures. The behavior of batteries in extreme situations (e.g. accidents) is also of interest.
The innovative research environment at the Battery and Sensor Test Centre pools the partners' expertise in the characterization and investigation of batteries with regard to their electrical and thermal properties under extreme loads. The following range of test benches with the corresponding load scenarios is currently available:
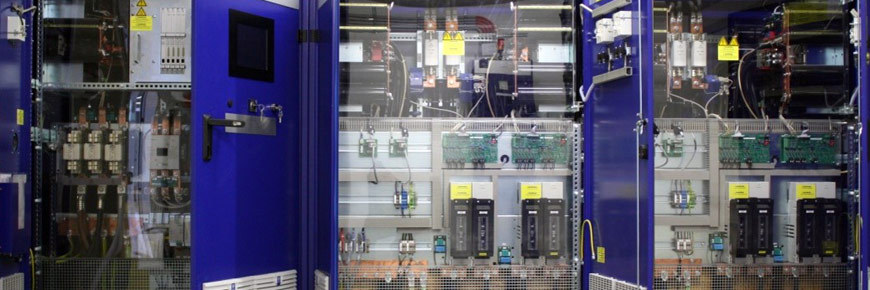
Dynamometer
The performance test bench enables electrical load tests up to 1000 V and 1,200 A (simultaneously), whereby the development of fire can also be tolerated.
With the dynamometer, a test environment has been created that is unique in this dimension. The test bench has current rise times of 10 to 90 percent in under 3 ms and is therefore also suitable for highly dynamic requirements. It can also be flexibly divided into two channels, each with an output of 600 kW.
The measurement infrastructure (see also below: Measurement sensors) enables dynamic data recording and a high control accuracy of the test bench to less than 0.1 percent.
Cost-optimized power supply via buffer battery
The high performance of the test bench is realized via a lead buffer battery, so that the grid is only minimally loaded and high energy or power prices can be avoided. A battery with 400 cells and an energy content of 800 kWh was installed for this purpose, which can provide up to 960 kW of power for around 20 minutes.
Measuring sensors: Electrical measuring system
The test bench includes a voltage measurement system with 320 channels with a total sampling rate of 20 kHz over 20 channels each. All channels are galvanically isolated from each other up to 1,000 V. The measuring range can be divided into decades from 10 V to 1,000 V in four ranges. The measuring system enables single-cell monitoring of a battery with up to 320 cells simultaneously. Additional current and temperature measurement values can also be recorded via freely configurable AD converters.
Measuring sensors: Fiber optic temperature measuring system
A fiber optic temperature measurement system enables the evaluation of almost any number of measuring points simultaneously, which can be flexibly integrated into battery systems or other test specimens. The big advantage is the small size of the sensors (about the thickness of a hair), so that they can be retrofitted into almost any existing system without any design changes. Secondly, the fiber optic sensors are insensitive to electromagnetic fields, which often lead to noisy measurement results in dynamically loaded battery systems. The sampling rate of the system is at least 1 Hz and the temperature accuracy is ±1 °C. A temperature range of -30 to 300 degrees Celsius is state of the art, temperature ranges up to the melting point of the fibers are still being further developed.
Climate chamber
A climate chamber measuring 3.0 m x 3.0 m x 2.3 m enables even larger vehicle batteries to be tested under controlled climatic conditions. This involves not only temperature influences but also the associated humidity. The humidity can be adjusted from 5 to 95 percent and the temperature can be regulated with a temperature change rate of 1 K per minute from -30 to 85 degrees Celsius. The climate container is fire-protected and has a nitrogen extinguishing system.
Cell and module test benches
The battery test center has a battery test stand with 16 channels, each with 6 V and 25 A, and one channel with 6 V and 400 A for testing single cells and modules. In addition, 8 channels can be paralleled as required from 25 A to 200 A to form a single channel. Also included are two fire-protected, water-cooled test chambers. With another module test bench (100V, 100A) also available at the EFZN and the power test bench, all battery sizes in the test field can be covered.
Kiln
Two combustion furnaces with internal dimensions of 3.0 m x 3.0 m x 2.5 m and 1.5 m x 1.5 m x 2.5 m provide an explosion-proof test environment for extreme tests, even on large-scale battery systems. In the event of an accident, for example, entire batteries can be burned down, with the remaining harmful gases being filtered out of the exhaust gas flow by means of a corresponding exhaust gas purification system. The furnace is temperature-stable up to over 1300 degrees Celsius and has a heating capacity of over 2 MW. The associated control system can be used to run standard temperature curves, for example, as are sometimes required for material tests. In addition, approval tests (e.g. fuel fire tests) can be carried out outdoors regardless of external weather conditions.
Gas measuring system
On the material side, various gas measurement systems enable the qualitative and quantitative detection of relevant combustion gases in the furnace exhaust gas flow. In addition to optical gas measurement systems, the Battery and Sensor Test Center also offers mass spectroscopy and other analysis methods in collaboration with the CUTEC Environmental Institute.